Una empresa de Valladolid, dedicada a la producción de perfiles de aluminio extrusionado, contacta con nosotros para que les ayudemos a diseñar un sistema de enfriado de las barras de aluminio que salen de la fundición.
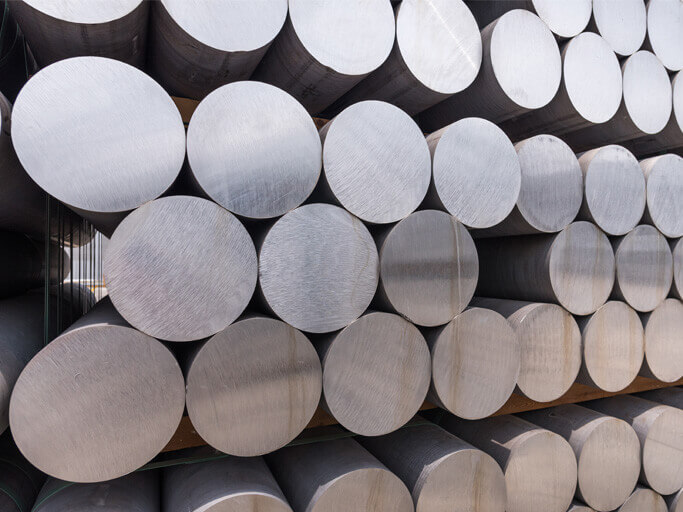
Tabla de contenidos
1. El problema
Una empresa de Valladolid, dedicada a la producción de perfiles de aluminio extrusionado, contacta con nosotros para que les ayudemos a diseñar un sistema de enfriado de las barras de aluminio que salen de la fundición. Las barras salen a una temperatura de 500ºC y se deben enfriar hasta tal punto que puedan ser manipuladas por los operarios sin tener que detener la producción.
2. Datos a tener en cuenta
Los perfiles son de 50 m de largo y tal como se ha indicado salen a una temperatura de 500ºC del horno a través de una cinta transportadora de rodillos a una velocidad de 14 m/s. El objetivo es enfriar estos perfiles lo más rápidamente posible para conservar todas las propiedades de dureza y elasticidad del aluminio, hasta tal punto que cuando la barra ha terminado de salir en toda su longitud, en el extremo más alejado del horno ya hayamos bajado la temperatura en 300Cº. Al concluir el recorrido por la cinta, con la barra ya a 200ºC, ésta pasa automáticamente a una plataforma deslizante, al final de la cual se cortará a las medidas que sea necesario y deberá estar a una temperatura máxima de 60ºC para permitir ser manipulada por operarios equipados con guantes protectores.
3. Determinación de las necesidades
En una instalación de estas dimensiones, son tantos los factores que intervienen que es muy difícil realizar un cálculo matemático que nos dé un resultado fiable de la instalación a realizar. En este caso y partiendo de experiencias anteriores, realizamos una primera instalación que posteriormente requirió pequeñas modificaciones para llegar al resultado final deseado.
4. La solución
Por la construcción de la instalación, ésta tenía dos zonas claramente definidas:
- ZONA A
Es la que se corresponde a la cinta transportadora de 50 m a la salida del horno y la que requiere una mayor concentración de aire para bajar la temperatura en 300ºC al final de la misma. Para conseguir este efecto procedimos a instalar, a la salida del horno, 4 ventiladores tubulares con una combinación de gran caudal y presión, a los cuales se les equipó con unas boquillas a la salida que concentraban un gran caudal de aire directamente sobre la barra de aluminio. A continuación se instalaron otros cuatro ventiladores tubulares de gran caudal, pero en este caso sin boquillas para crear una corriente envolvente alrededor de la barra. Para completar el soplado sobre toda la superficie de la misma, por debajo de la cinta transportadora se instaló un sistema de ventilación en el que a través de un conducto con aberturas e impulsado por un ventilador centrífugo, se soplaba aire de abajo a arriba para enfriar la base de la barra.
- ZONA B
En esta zona, que es una plataforma deslizante en la cual las barras no circulan en sentido longitudinal sino transversal, se instalaron dos baterías de ventiladores soplando de abajo a arriba, una en sentido opuesto a la circulación de las barras y la otra en el mismo sentido, para incidir sobre cada una de las caras laterales y sobre la base. En este punto ya estábamos en el objetivo señalado de 60ºC pero, como mejora, al final de la plataforma y antes de llegar a la zona de corte, se instaló un ventilador centrífugo de media presión con cuatro boquillas para soplar en el interior de las barras y liberar el calor latente que pudiese quedar dentro de las mismas, consiguiendo reducir la temperatura a casi la mitad.
Consulta el caso práctico completo «Ventilación Fábrica de Extrusión de Aluminio» en el que encontrarás los productos recomendados y sus características técnicas.